If you’re looking for ways to be around aircraft and in demand in the aviation industry, becoming an Aviation Maintenance Technician (AMT) could be an opportunity for you to explore. On the other hand, if you decide to become an aviator, you will spend plenty of time working with aviation mechanics. These highly trained people will make sure that your aircraft operates safely and efficiently.
In addition to their mechanical workings, AMTs will also learn about the materials that are used to make aircraft. Some of the most training-intensive and labor-intensive substances used in aircraft are called “advanced composites.” These are the combined materials that make aircraft light and strong. They also resist the fatigue and corrosion issues that metal parts can develop.
What is a composite and what makes it so advanced? Let’s look to the Essentials of Advanced Composite Fabrication and Repair for a definition:
Composites are comprised of two or more materials working together, where each constituent material retains its unique identity within the composite and contributes its own structural properties, yet upon combination the resulting material has superior properties to those of its constituents. A good example of an everyday composite material is concrete. Concrete is made with select amounts of sand, aggregate, and perhaps even glass fiber mixed with cement to bind it together. If the concrete were broken open, the individual constituents would be visible. The type and quantities of these individual constituents can also be adjusted to give the resulting concrete different properties depending on the application.
Starting in the 1930s (when fiberglass was first patented), people began experimenting with composites to make vehicles lighter. First boats, then Corvettes, helicopter blades, and even water-skis. Those used in airplanes are composite laminates. They combine fibers and a matrix material that binds the fibers together. For example, fiber-reinforced polymer (FRP) composites have short glass fibers in a polymer resin matrix. Materials like these are found in bathtubs, pools, doors, car fenders, and construction materials like wall panels, corrugated sheets, and skylights (Figure 1).
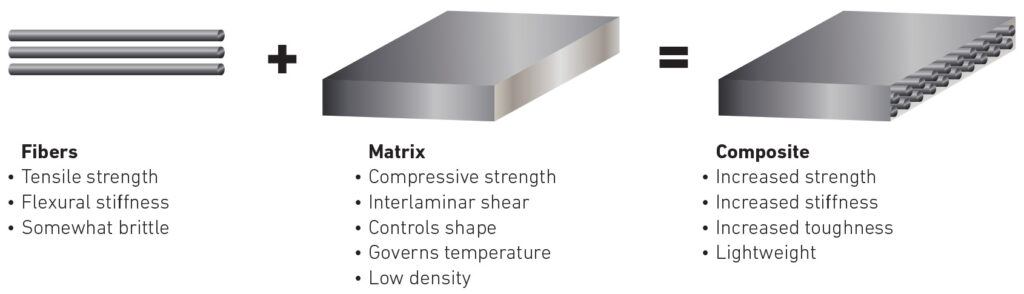
Any composites that are expected to be under a high load have continuous or long-fiber reinforcement. This transfers the load along bundles or layers of fibers that are arranged to run the length and width of the structure—think of the layers in a sheet of plywood. You’ll find this type of composite laminate in bridges, snowboards, bicycle frames, race cars, and spacecraft structures—as well as aircraft.
Turning to advanced composites, let’s go back to Dorworth and Gardiner (terms in bold italic are defined at the bottom of the page):
“Advanced composites” are generally considered to be those that use advanced reinforcements such as carbon, aramid, and S-2 glass fibers that exhibit high strength-to-weight ratios. They are typically more expensive, with more precisely tailored properties to achieve a specific objective.
Fiberglass vs. Advanced Composites
Some composites are generally referred to as “fiberglass” due to their use of randomly oriented, chopped glass fiber (E-glass) and polyester resin, whereas most aerospace structural parts are made using precisely laid plies of carbon fiber/epoxy prepreg, an example of advanced composites (Figure 2).
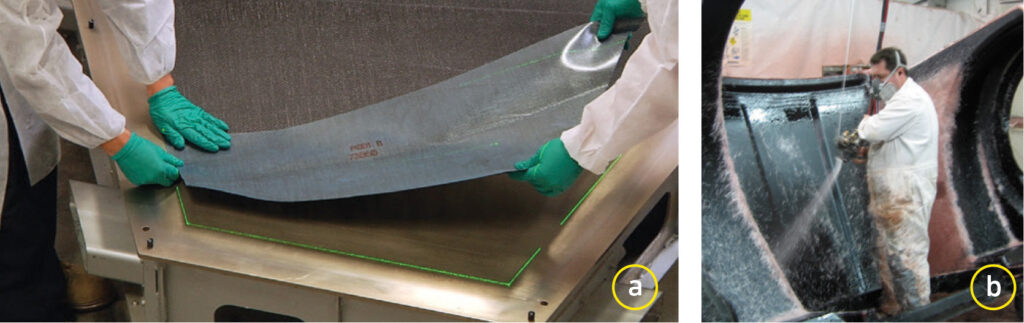
According to Essentials of Advanced Composite Fabrication and Repair, you can find these specialized materials in many areas of an aircraft, including the following:
Large components of commercial airliners—such as the vertical and horizontal tail plane (stabilizer) on the Airbus A320, A330/340, A380 and Boeing 777, the wing, center wing box and fuselage for the Boeing 787 Dreamliner and Airbus A350, and various structures on many smaller craft such as the wings for the Bombardier C Series airliners (Figure 3).
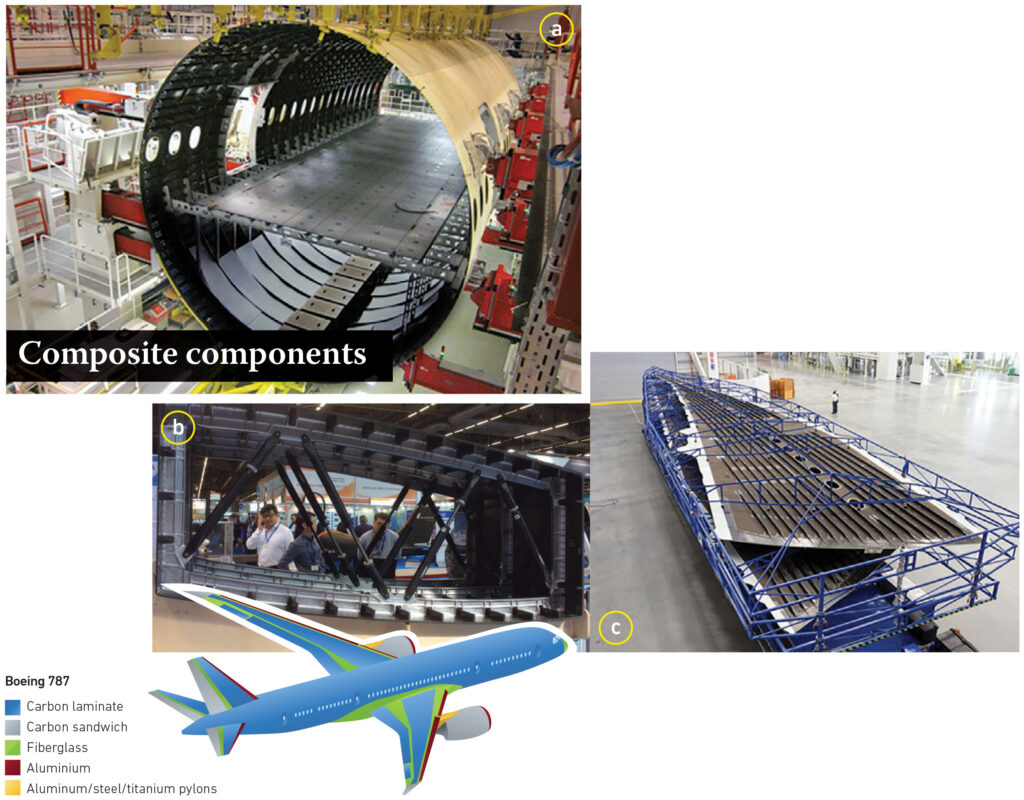
Large primary structures on military aircraft—such as the wing and cargo doors for the Airbus A400M transport, fuselage/wing for the B-2 Spirit Stealth Bomber, rotor blades and aft fuselage for the V-22 Osprey tilt-rotor, as well as the most of the fuselage and wings for the F-22 Raptor and F-35 Joint Strike Fighter (Figure 4).
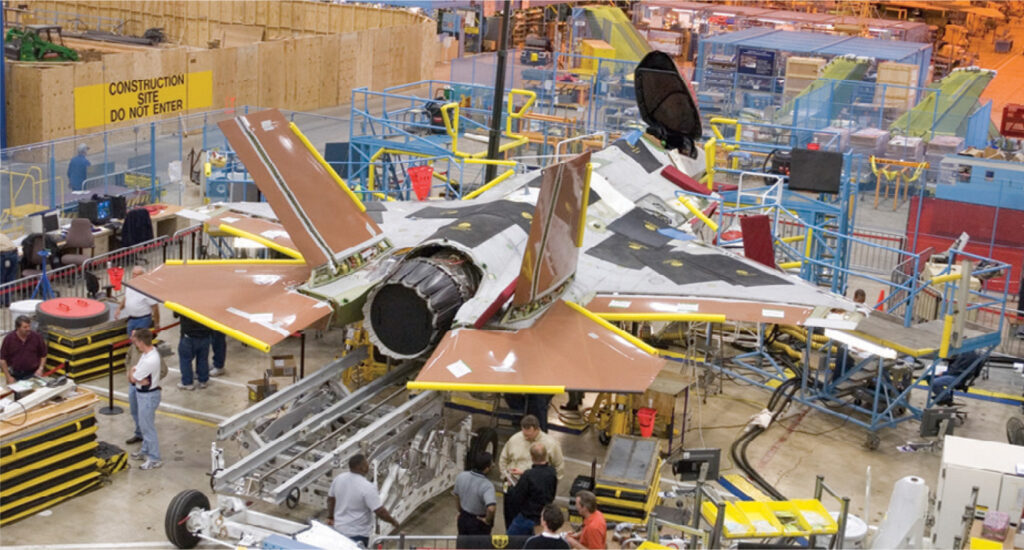
Many other components on modern airliners—such as radomes, control surfaces, spoilers, landing gear doors, wing-to-body fairings, passenger and cargo doors, trailing edges, wingtips and interiors (Figure 5).
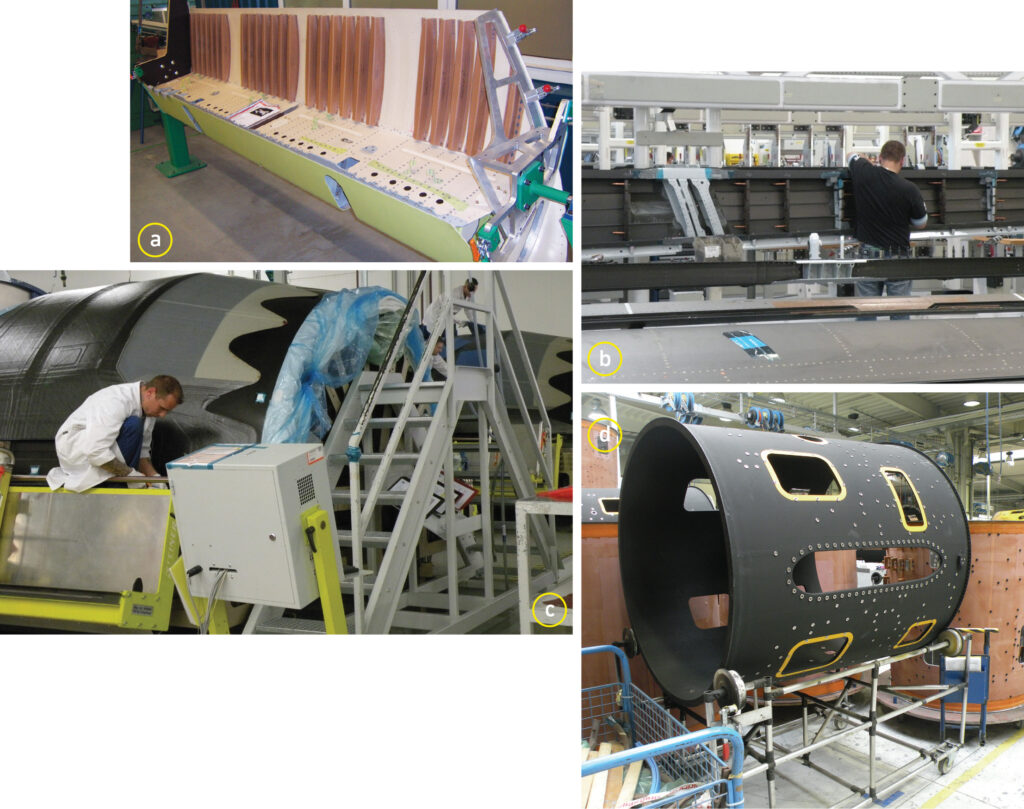
Primary components on helicopters and other vertical takeoff and landing (VTOL) vehicles also make use of advanced composites.
Rotor blades and rotor hubs have been made from carbon fiber (CF) and glass epoxy composites since the 1980s. Composites can make up 50 to 90% of a rotorcraft’s airframe by weight, including radomes, tail cones and large structural assemblies (Figure 6). For example, Bell Helicopter Textron’s 429 corporate/EMS/utility helicopter features composite structural sidebody panels, floor panels, bulkheads, nose skins, shroud, doors, fairings, cowlings and stabilizers, most made from CF/epoxy.
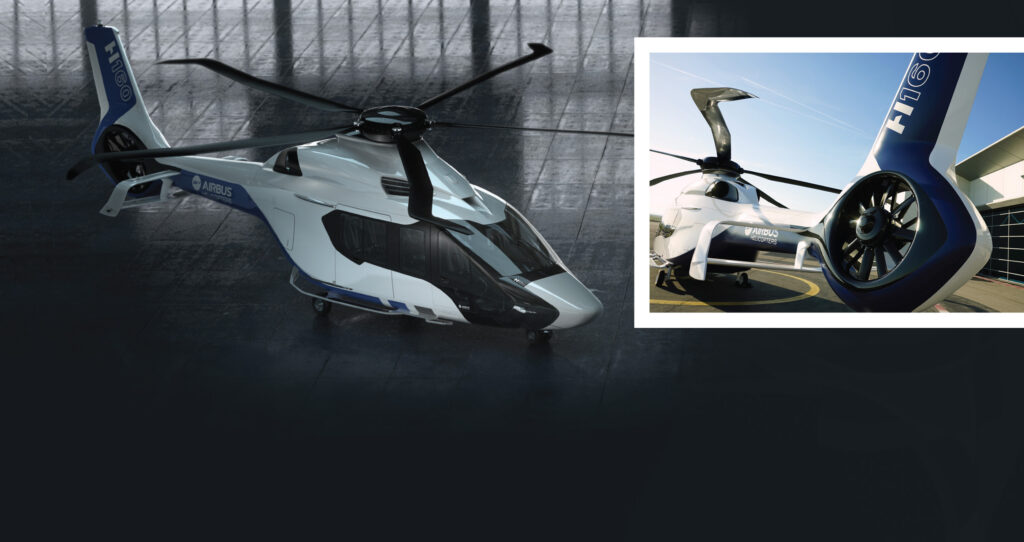
The applications seem endless. Sporting goods, such as bikes, tennis rackets, and golf clubs have taken advantage of carbon fiber for decades. Their automotive applications range from driveshafts in race cars and high-end sports cars to leaf and coil springs in higher-volume models. You can find them in the roofs of BMW’s M3 and M6 models as well as the hood and fenders for Corvette’s LeMans Commemorative Edition Z06.
They have found their way into medical devices, civil engineering structures, large marine vessels, wind turbine rotor blades, missiles, and even space vehicles, such as the James Webb Space Telescope (JWST), which uses a carbon fiber reinforced backplane structure and sunshield booms.
If you want to learn more about how composites are used, how they’re made, or how they are tested and repaired, pick up the new edition of Essentials of Advanced Composite Fabrication and Repair, or A Comprehensive Guide to Composites at the ASA website. Or, take your new-found knowledge and discuss it with the nearest AMT.
Definitions
Aramid is short for “aromatic polyamide.” They are known for high tensile strength, low density, and resistance to impact, heat, and degradation. You may have heard of one of the best-known aramids—Kevlar.
S-2 glass is high strength and has a higher percentage of silica than other types of glass (e.g., the more widely used E-glass). It is used when tensile strength is most important.
Prepreg is a material that has been saturated with matrix material in advance—thus pre-impregnated.
Figures from Dorwith and Gardiner, Essentials of Advanced Composite Fabrication and Repair. Featured image photos by thisisbossi, Brett Jordan, and Roman Kaiuk.